First published November 2015
Learn about the different types of air circulation fan plus key aspects of fan energy efficiency, installation cost and payback.
Quick links:
- What circulation fans can and cannot do
- How to optimise energy efficiency
- The different types of air circulation fans
- Pros and cons of different fan types
- The economics – a worked example
What circulation fans can and cannot do
Circulation fans have been widely used in greenhouses for many years. A well designed fan installation will benefit the greenhouse climate by helping to maintain consistent temperature and humidity throughout the growing area. The gentle movement of air over the leaf surface is also an aid both to transpiration and the distribution and uptake of CO2. Fans also contribute to a more pleasant working environment. Used in conjunction with low volume sprayers, fans ensure more even distribution of plant protection products.
While circulation fans can play a part in creating uniform temperature and humidity throughout the growing area, it is important to understand that fans have no effect on the moisture content of the air. Removing moisture is only possible by introducing cooler, drier air from outside or dehumidification.
How to optimise energy efficiency
Key performance and energy efficiency points to consider when installing and operating your circulation fans.
Air circulation fans should be operated on the principle that air can be moved using only enough energy to overcome friction losses and turbulence. Air is heavy and difficult to get moving, so persistence of air movement rather than speed is the key to achieving a uniform greenhouse environment. From an energy perspective, it’s more economical to move large amounts of air at low speed and pressures, although by no means all fans are designed with this in mind and, unless fitted with speed control, will operate at high speed with little regard to operational costs.
Designing a suitable fan system that compliments rather than conflicts with the heating and ventilation systems in a greenhouse requires considerable experience. In general the objective should be to install a system that is capable of circulating the entire air volume in the greenhouse between 1 and 2 times per hour.
Saving energy
When temperature and humidity throughout the growing area are consistent, there is less risk of condensation which reduces the risk of fungal diseases as well as the need for excessive pipe temperatures, and so potentially reduces energy consumption even further.
Since January 2015, fans with an electrical input of between 125W and 500W are subject to the ErP directive which sets standards for efficiency. You should ensure that any fan system being considered meets the ErP criteria.
Fans should be fitted with variable speed motors which can be modulated automatically and thereby save energy.
For growers with climate computers, further energy saving is possible by controlling fans in conjunction with vent position so that the fans are switched off completely when the vents are open sufficiently to ensure good air movement.
The different types of air circulation fan
A look at three different types of air circulation fan, horizontal, air tubes and vertical, plus typical configurations for serial and parallel ventilation.
Developments in greenhouse design, the advent of higher structures, the ErP directive and the widespread adoption of new growing methods such as hanging gutters and mobile benches have led to changes in fan technology, design and application.
There are three popular and quite different approaches to air circulation in modern horticulture.
Horizontal air movement fans
These are generally installed well above the crop with fans either side by side blowing in the same direction (parallel fans) or in alternate lines blowing back and forth along the bay length (serial fans) – see Figure 1. They often have a dual purpose for ensuring the even distribution of low volume chemicals applied by systems such as Enbar.
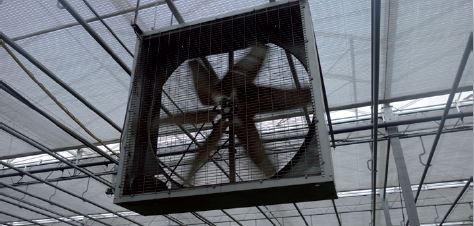
Air tubes
Air tube systems generally employ conventional horizontal fans attached to perforated polythene ducts running the length of the bay or row. Air is transported along the tube and out through the perforations to ensure a gentle air flow throughout the length of the tube or duct. They are primarily designed for mounting beneath hanging gutters and mobile benches.
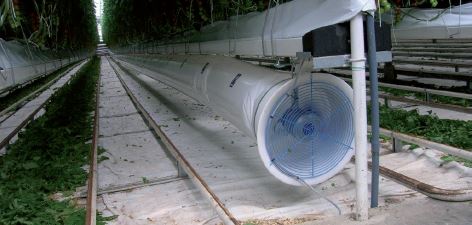
Vertical fans
Vertical fans have not so far been widely installed in the UK, but as a result of the increasing popularity of higher greenhouses that may change. As a vertical fan mounted well above the crop will move warm air from the top of the greenhouse to create a more even vertical temperature distribution.
In a recent variation, an air tube can be attached to the fan outlet so that the warm air above the fan is transported through the tube to ground level (usually below benches or gutters).
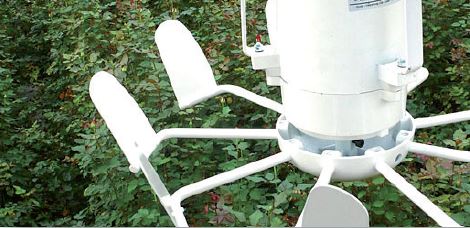
Typical configurations
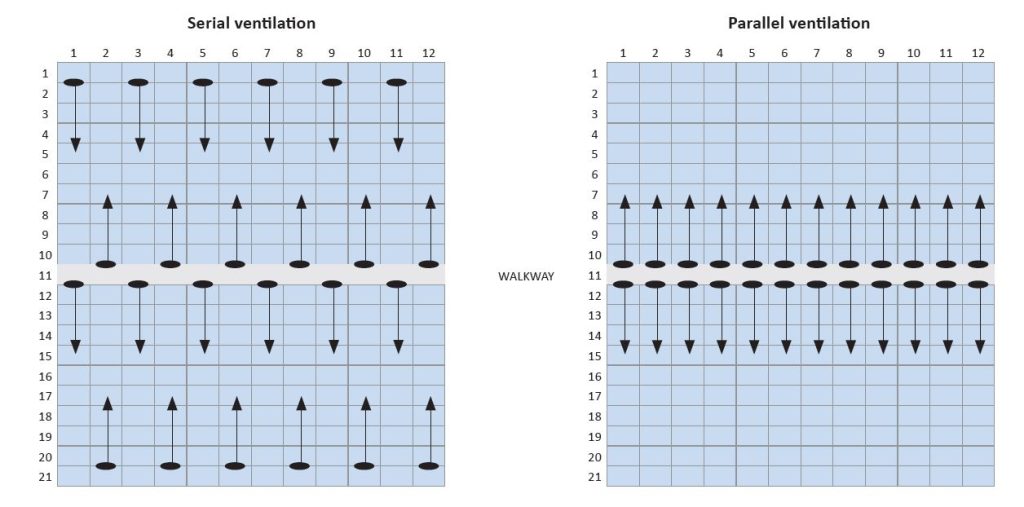
In this example, 24 fans delivering 5,500 m3/hr will turn over the greenhouse air approximately 2.2 times per hour.
Pros and cons of different fan types
How effective are the different fan types at creating effective air movement and even distribution of temperature, humidity and CO2 throughout the crop?
Having been available in greenhouses for many years, horizontal fans are widely used and understood. They are not thought to be as effective at correcting vertical temperature differences as air tubes or vertical fans. In glasshouses already fitted with a thermal or shade screen and apex seals, horizontal fans may not improve the consistency of the climate a great deal more, though the crop will still benefit from the active climate created by the gentle movement of air.
Air tube systems are now very popular in salad crops with hanging gutters and under mobile benches. Properly designed and installed, air tube systems are effective at equalising temperature and humidity both horizontally and vertically because negative pressure at the fan inlet and the gentle air flow created by the perforations along the tube or duct create effective air movement and even distribution of temperature, humidity and CO2 throughout the crop.
Vertical fan systems are relatively new, so there is much less experience with their application. It should not be assumed that vertical air movement will necessarily create more even temperature and humidity vertically than a horizontal air tube system until proper comparisons become available. Nevertheless, vertical fans may have advantages in some applications:
- Under sodium lamps when it is important to move the heat generated by lamps in the roof of the greenhouse into the crop.
- In vine crops grown without gutters or in the soil.
The economics – a worked example
A worked example of costs and payback for an energy intensive salad crop such as tomato or cucumber.
Energy intensive salad crop
Here is a worked example for an energy intensive salad crop such as tomato or cucumber.
In this case it is assumed that the annual heating energy consumption is 600kWh/m2 and the area is 10,000m2 (1Ha).
Fan Capital Costs
Assuming that the capital and installation costs are financed over 24 months at 6% interest rate.
Annual purchase cost = £3,723.00
Fan Operating Costs
Electricity for fan operation = 20 fans x 0.24kW x 2250hrs x £0.08p/kWh = £864
Annual maintenance = £100
Total = £964.00/year
Heating Costs
Annual heating costs = 600kWh/m2 x 0.02p/kWh x 10,000m2 = £120,000/Ha/year
Payback assessment
In the first two years after installation, the total additional cost for the air movement system will be £3,723 + £964 = £4,687.
To provide payback this cost must be offset against energy savings that may be secured.
Therefore, an energy saving of £4,687/£120,000 = 3.9% must be achieved if payback is to be achieved inside two years.
Based on a growing temperature regime of 20˚C day/18˚C night and assuming typical UK weather conditions, it is commonly accepted that a 1˚C error in temperature control is equivalent to 5% energy waste.
Elimination of a 1˚C error in glasshouse temperature by using fan air circulation will therefore ensure a payback inside two years.
Note costs used correct as at September 2015.