Traditional CO2 Usage
Certain protected crops are commonly dosed with CO2 to benefit crop growth and improve yields. Traditionally, CO2 is delivered via one of three methods: natural gas fired boiler, natural gas fired CHP (combined heat and power), or vaporisation of liquid pure CO2.
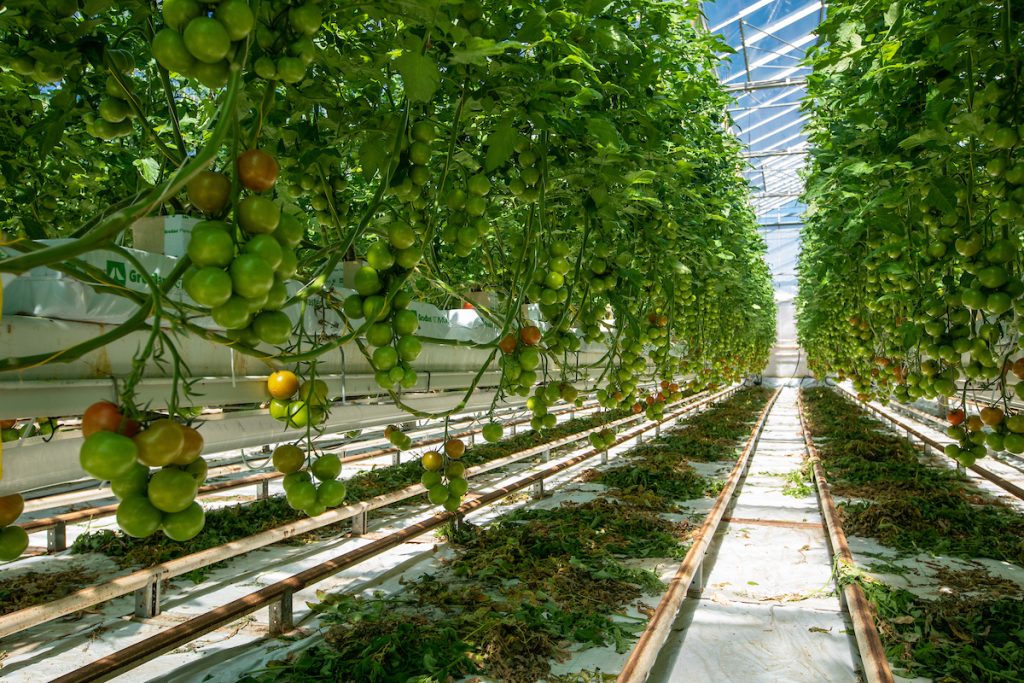
© Gary Naylor Photography
Natural gas boilers are common on protected horticultural sites due to their efficient heat delivery, relatively cheap capital costs, and ease of operation. CHP is also common on protected horticultural sites which are paired with a large electricity load; crop lighting, chilled storage, or packhouse operation. On sites with minimal heating load (or those with non-fossil fuel-based heat delivery such as heat pumps), pure CO2 is used. Pure CO2 is typically sourced from industrial processes.
The following table outlines the inputs, costs, and outputs to produce 1 tonne of CO2 from these sources:
Technology | Inputs | Input Costs[1] | Co Products |
Natural Gas Boiler | 5,489 kWh gas | £189.13 | 4,665 kWh heat |
Natural Gas CHP | 5,489 kWh gas | £189.13 | 2,305 kWh heat |
2,470 kWh electricity | |||
Pure | Delivered via tanker + 160 kWh heat to discharge | Between £150 – £1500 to purchase plus £30 to discharge | None! |
To read more about how CO2 is conventionally produced read our technical update from 2017.
Current gas prices and the associated cost of CO2 may make you consider different methods of producing CO2. Although alternative sources have been discussed in the past, there is clearly a greater value in CO2 than there previously was, which changes some of the economics. Understandably, the question of alternative CO2 sources has arisen again – Read on to learn about 5 alternative options of sourcing CO2 for you to consider.
Biomass sources of CO2
CO2 sourced from biomass comes in two general categories: dry and wet. Dry biomass refers to traditional biomass fuel used in boilers, gasifiers, or pyrolysers (wood, straw, perennial energy crop, etc.). Whereas wet biomass most commonly refers to anaerobic digestion (AD).
1. Biomass boilers
Other than natural gas boilers and CHP, the most common heating systems found at horticultural sites are biomass boilers. Incentivised by the Renewable Heat Incentive (RHI), these systems are particularly common alongside traditional gas systems, to provide ancillary heating and incentive payments. Although, single biomass systems do exist.
Systems do exist on a proven scale to extract CO2 from biomass boiler flue gas, however, the main concern is that the flue gases contain a much higher proportion of pollutants such as NOx, SOx, and particulates, etc. compared with natural gas combustion. This means that the complexity and cost of CO2 capture from the flue gas is much higher than natural gas combustion. Additionally, when biomass boilers are sized for ancillary heat delivery, their CO2 delivery rate is likely to be low. The amine-scrubbing CO2 collection from biomass combustion necessitates boiler capacities around 5MW to be financially viable.
Gasification and pyrolysis are similar processes to one another; thermal degradation of material into syngas (a mixture of hydrogen (H2), carbon monoxide (CO), CO2, and other gases in small quantities) and char (predominantly carbon); the difference between the two is the amount of oxygen present during the reaction. The syngas itself does not produce much CO2 when combusted, but between 15-20% of the syngas is already CO2, which can be harvested directly. Additionally, the CO can be reacted with water using gas reforming to produce further H2 and CO2.
2. Anaerobic digestion (AD)
AD is the biological decomposition of material in a low-oxygen environment, producing biogas (roughly 50-60% methane and 40-50% CO2, with small amounts of H2S and other gases depending on feedstock used) and digestate (a liquid mixture of digested material). Biogas can either be combusted directly, or ‘upgraded’ into grid-ready biomethane by stripping CO2 and adding propane (propanation) to meet grid standards.
The issue with harvesting CO2 from biogas is that it typically contains H2S in quantities ranging from 0.5% – 5%. H2S is extremely corrosive when burned and is typically filtered out prior to combustion. Occasionally, some of the other non-methane gases are removed from raw biogas prior to combustion to improve efficiency, but this is not a common practice.
How do they compare?
The following table outlines the inputs and outputs from boiler combustion of biomass, syngas, and biogas, required to produce 1 tonne of CO2:
Fuel | Inputs | Typical costs of inputs | Outputs |
Biomass | 2,609 kWh wood | 750kg woodchip – £100 | 2,087 kWh heat |
Syngas | 8,488 kWh wood[2] | 2,122 Kg woodpellets – £400 | 4,690 kWh heat |
810 m3 CO | |||
Biogas | 25 tonne feedstock | Between £0 and £1,250 | 2,747 kWh heat |
23 tonne digestate |
These data highlight that biomass or biogas combustion plants can be sized at nearly half the capacity of natural gas combustion plants to achieve similar CO2 production rates. For sites with existing biomass boilers accredited on the RHI, this presents an opportunity to install sophisticated CO2 capture equipment.
When upgrading biogas to biomethane, H2S and volatile organic compounds are stripped, leaving a stream of ‘clean’ methane which goes on to propanation, and ‘clean’ CO2 which is typically vented to atmosphere.
There is clearly a market for AD operators to capture pure CO2. Biomethane is a more likely avenue than biogas for several reasons: new biogas combustion installations do not gain benefit from any incentive schemes; they tend to be smaller systems and therefore have less CO2 resource; and less capital is involved in setting them up, meaning that the couple of million pounds of additional CO2 cleaning, capture, and liquefaction equipment would be a greater proportion of the total cost. Conversely, new biomethane installations can benefit from incentive schemes such as the Green Gas Support Scheme and Renewable Transport Fuel Obligation, and biomethane plants are necessarily large multi-million-pound projects with high CO2 resource.
Additionally, biomethane sites handling certain types of waste have historically struggled with poor market perception, where companies do not want to use the CO2 in the food and drinks industry due to its waste origin, despite purity.
The following table outlines the feedstock tonnages and gas flow rates required to produce 1 tonne of CO2 from AD.
Feedstock | Tonne Input | kWh Biogas Output |
Energy Crop | 7 | 5,896 |
Food Waste | 14 | |
Animal Waste | 55 |
The size of AD installation required to produce meaningful amounts of CO2 is large, in the order of 7 MW gas output (i.e., 9 tonnes/hour energy crop use, 17 tonnes/hour food waste use, or 65 tonnes/hour animal waste use). This is larger than what is practically possible for a horticultural business to operate without significant area and staff diversification. Instead, as the AD industry is likely to expand in the coming years, it may represent a more sustainable source for pure CO2.
Chemical sources of CO2
There are also chemical sources of CO2 worth considering: Steam Reforming (SR) and hydrocarbon fuel cells.
3. Steam Reforming (SR)
When discussing CO2 potential from biomass gasification/pyrolysis, we highlighted that syngas tends to have a high CO content: anywhere between 20-60% by molecular composition. Although it is not a common process, CO can be further reacted with steam and a catalyst to produce additional H2 and CO2. This process is essentially the second half of SR, known as a water-gas shift reaction. The reaction requires steam between 200-450°C (depending on the catalyst used), and the high equipment and energy costs are the reasons why water-gas shift reactors are not common on smaller-scale biomass gasification/pyrolysis installations.
Rather than gasification/pyrolysis, SR produces syngas from a hydrocarbon fuel (typically natural gas) by reacting with high pressure (14-40 bar), high temperature (800+°C) steam. The syngas is ‘cleaner’, since the input fuel has fewer impurities, meaning both the H2 and CO2 have very high purity. This is the most common process of producing ‘grey’ and ‘blue’ hydrogen.
Due to the high H2 product purity, SR is the most common way to produce synthetic ammonia, meaning it is behind much of the liquid CO2 already used on horticultural sites!
The following table outlines the typical inputs and outputs from SR of methane, required to produce 1 tonne of CO2. Methane has been chosen here because it is the most efficient and common fuel for SR.
Inputs | Outputs |
1,100 kWh heat | 200 kg H2 |
5,646 kWh CH4 | |
800 kg water |
There is a very high cost associated with this process, and the high pressures and temperatures required do not lend themselves to small installations. To be profitable, both H2 and CO2 must have a very high value. If large industrial fertiliser producers have chosen to shut down due to the increased energy costs, it seems unlikely that this SR is a practical or appropriate option for horticultural sites at present.
However, it is worth noting that H2 is gaining in value as a fuel or an energy storage medium, and gas has reduced in cost through the early months of 2023. In the near future, these economics may shift. If industrial SR facilities are opened to produce H2, there may be potential opportunities to locate horticultural sites close to these facilities to make use of the produced CO2.
4. Hydrocarbon fuel cells
A fuel cell is a type of generator that transfers the chemical energy stored in the fuel into electrical energy with heat as a by-product. To sustain this reaction, a constant flow of fuel and oxygen is needed.
H2-fuelled are the most common type of fuel cell undergoing development, because they can be used with ‘green hydrogen’ for long-term renewable/low-carbon electricity storage. As well, the H2 vehicle market and H2 production subsidies have encouraged development. However, other fuels such as hydrocarbons and alcohols can also be used in fuel cells.
Methane has potential here, as the outputs from the reaction are electricity, heat, CO2, and H2O. Methane fuel cells are generally high-temperature types, meaning that the heat generated can be used with traditional high-temperature heating infrastructure.
To gauge its effectiveness, it can be compared directly with natural gas-fired CHP. The following table outlines comparative figures for producing 1 tonne of CO2 via natural gas-fired CHP and methane fuel cells:
Technology | Capital Cost £/kW | Inputs | Outputs |
Gas-fired CHP | 600 – 1,000 | 5,489 natural gas | 2,470 kWh heat |
2,305 kWh electricity | |||
Methane Fuel Cell | 1,500 – 4,000 | 5,646 kWh CH4 | 1,976 kWh heat |
2,823 kWh electricity |
Natural gas from the UK transmission grid is not pure CH4; it contains other hydrocarbons, primarily propane. There are also plans to blend in up to 5% hydrogen into the UK gas grid by 2025.
While electrical efficiency is higher for fuel cells, thermal efficiency is slightly lower. Total efficiency is similar, around the 85 – 90% range (however, this will depend heavily on the type of fuel cell used. Electrical efficiencies as high as 70% are possible in some types).
Not shown in this table is the purity of the CO2 produced. Natural gas combustion produces non-useful gases such as CO and NOx. The table above illustrates complete combustion, meaning that any CO produced will reduce the amount of CO2 produced. While exhaust gas from CHP is filtered before going through a glasshouse, there is still pollutant present. Conversely, the lower operating temperatures of fuel cells and lack of N2 in the process stream discourage and sometimes eliminate NOx formation entirely. This is a large benefit, as no flue abatement equipment is needed.
The costs for fuel cells are currently prohibitive. However, consistent research and development will change that. The department for business, energy and industrial strategy (BEIS) suggests that by 2030, fuel cells could drop to the £1,000/kW mark, which would put them in competition with smaller-scale CHP cost. It is worth noting that fuel cells are much less prone to failure and incur far less operation and maintenance costs than a gas-fired CHP. However, this does not outweigh the capital costs at present.
5. Direct air capture of CO2
In principle, direct air capture (DAC) CO2 has been around for many years; pioneered to maintain environmental conditions aboard spacecraft. However, commercial maturity of the technology is still low, and many DAC installations are focused on large-scale and long-term storage of CO2 and selling the associated carbon credits.
As highlighted in the previous technical update, the price for generating CO2 via traditional methods has increased significantly, leading to availability issues and further increased prices for the user. Additionally, pressure around greenhouse gas (GHG) emissions, and an expectation that natural gas combustion will be somehow disincentivised in the near future, has driven innovation in this sector.
While attending the Greentech Conference earlier in 2023, there were two notable examples of DAC CO2 technology being trialled for use in horticulture: by Airbus and Skytree. Each of these are developing units which are planned to be commercially available in the coming year(s).
DAC CO2 works by passing ambient air through a sorbent material, which adsorbs a portion of the CO2 in the air. To release the captured CO2, the sorbent is heated. With the materials used in these units, the required temperature is only around 90°C, so they can be easily integrated with many existing horticultural heating systems.
One downside is that the sorbent material is not permanent; after around 30 months of use it must be replaced. When used in enclosed growing systems (which these DAC units are designed for), this means that it must be replaced after around 2.5 years of use. However, in 6-month CO2 dosing cycles common in UK glasshouse production, this means the sorbent can last for around 5 years. At this stage, the costs and availability of the sorbent material is not clear.
Absorption is when a chemical is captured within another substance, whereas adsorption is when a chemical is captured on the surface of another substance.
We were able to set up a meeting with Skytree to discuss some of the details of the Skytree Cumulus, the first small footprint unit that produces 10kg of CO2 per day, which they are launching for vertical farms. This will be followed by a larger 10ft container unit, the Skytree Stratus, providing 200kg of CO2 per day.
Although designed for and tested in enclosed vertical farming systems, particularly container and tower farms, the DAC units are modular, i.e., several units can be installed to reach the desired CO2 dosing rate. The following figures focus on the Skytree Stratus model, as this would be most appropriate for rollout in larger glasshouse operations.
Given a flow of ambient (~400ppm CO2) air, producing 1 tonne of CO2 requires energy consumption in the order of 1,700kWh; Skytree’s target for the Stratus model is that 90% of that energy will be heat and 10% electrical. Multiple units would be installed to reach the desired daily CO2 dose rate. To contextualise the cost of running DAC units, we calculated the following scenarios*, each generating 1 tonne of CO2:
Boiler | CHP | DAC[3] | Boiler + DAC | CHP + DAC | |
Gas use (MWh) | 5.49 | 5.49 | – | 1.36 | 2.10 |
CO2 from gas (tonne) | 1.00 | 1.00 | – | 0.25 | 0.38 |
Heat from gas (MWh) | 4.67 | 2.47 | – | 1.15 | 0.94 |
Elec from gas (MWh) | – | 2.31 | – | – | 0.88 |
DAC heat use (MWh) | – | – | 1.53 | 1.15 | 0.94 |
DAC elec use (MWh) | – | – | 0.17 | 0.13 | 0.10 |
DAC CO2 (tonne) | – | – | 1.00 | 0.75 | 0.62 |
Total CO2 (tonne) | 1.00 | 1.00 | 1.00 | 1.00 | 1.00 |
Cost (£)[1] | 189 | 189 | 171 | 60 | 72 |
Value (£)[4] | – | 232 | – | – | 78 |
Some of these figures are quite compelling for glasshouse growers. Particularly since the majority of CO2 dosing occurs when heat is not required during warmer months, meaning the heat produced when generating CO2 from a gas boiler/CHP has no value.
An additional benefit of DAC integration is a reduction of carbon emissions onsite. Unlike natural gas combustion, which increases the net CO2 in the atmosphere and contributes to your business’ carbon footprint, DAC captures ambient CO2 which produces zero net emissions. This means the only emissions are those associated with generating the heat and electricity to power the DAC unit, much less than burning gas. This can be seen in the table above, where 75% less gas is used in a boiler + DAC, or 62% less using CHP + DAC, to produce the same CO2 as those technologies alone.
[1] Based on average day-ahead gas/electricity market prices available so far throughout 2023, commodity price only: electricity – £100.65/MWh; gas – £34.46/MWh.
[2] Highly variable with fuel quality, production temperature range, oxygen availability during gasification, etc. This figure also assumes that CO is stripped prior to combustion for further hydrogen production.
[3] With electrical heating.
[4] Assuming all CHP-generated power is exported to the grid.
This article was written by Eirinn Rusbridge.