First published February 2017
We look at the alternative sources of CO2 supply from biomass and anaerobic digestion and discuss how they have developed since the uptake of renewable-based heating systems.
Quick links:
- A developing picture
- CO2 from biomass combustion
- CO2 from biogas
- CO2 from biomass gasification
- CO2 from bio-methane conditioning
An ever developing picture
Novel methods of CO2 recovery are emerging, such as CO2 from biomass and biogas treatment. However, these technologies are in their infancy and will be constrained to certain sites. The renewable incentives associated with these methods of heat or gas generation are significant and could help bolster the uptake of the high capital cost, but relatively low running cost, of CO2 recovery for these methods.
In Conventional sources of CO2 we look at the conventional sources of CO2 supply and discuss the influence of factors, such as heat requirement and electricity price on the cost attributed to CO2 supply.
CO2 from biomass combustion
An explanation of biomass combustion as a source of CO2, including how to clean the gas from the boiler in order to produce the required quality of CO2.
Straightforward biomass combustion represents by far the largest proportion of new CO2 source potential in commercial horticulture. Although anaerobic digestion, biogas production and gasification have also emerged as potential sources, biomass boilers have seen the highest level of adoption.
Whilst there is a broadly equivalent quantity of CO2 in biomass combustion flue gases compared to fossil fuels, the cleanliness of the gas direct from the boiler is much more of a problem and this presents the biggest challenge to users. Therefore, gas cleaning equipment is required to produce the necessary quality of CO2. The two approaches to this are to either remove the pollutants and leave clean CO2, or to extract the CO2 and discard the remaining pollutants. The ideas sound similar but, in fact, employ different techniques.
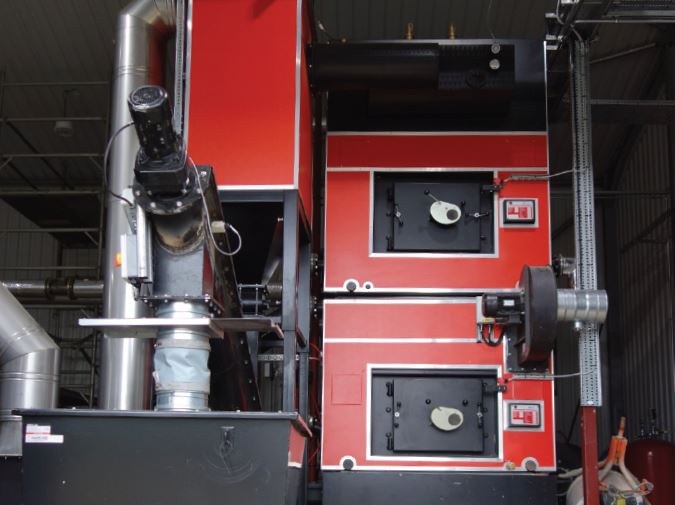
How to remove the pollutants
Table 1 describes the major pollutants from biomass combustion and the techniques available to remove them. One of the biggest issues with selectively removing the pollutants is that the particulate matter can block other parts of the system, such as catalytic media, rendering them useless.

How to extract the CO2
The alternative to selectively removing the pollutants is to extract the CO2 directly. The most common method is to use an amine scrubber. This was the principle introduced in a Canadian system, developed in late 2013 (ProCeed), and which has subsequently been adopted by a small number of companies in the UK and Europe.
For the system to work well, high temperature flue gas must be supplied by the boiler, substantially higher than the 95°C common to most hot water biomass boilers. This means that retrofitting the gas cleaning equipment on such systems is not viable.
The capital cost of this equipment is very high, but running costs are relatively low once installed. For example, a system capable of delivering 500kg CO2/hr would cost approximately £1 million. Indicative running costs for this type of system are around £20 per tonne of CO2.
With support for biomass boilers from the Renewable Heat Incentive, a biomass system with CO2 recovery can be a financially viable alternative to a conventional heating/CO2 system.
Note costs and data used are correct as at March 2017.
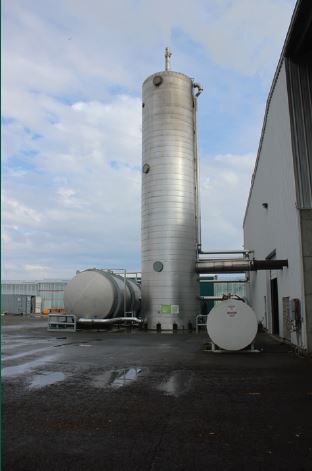
CO2 from biogas
How CO2 can be recovered from biogas produced by anaerobic digestion and the effect of the flue gas impurities in raw biogas on plants.
Biogas is produced from the anaerobic digestion of biological matter. Burning biogas to produce heating for glasshouses is eligible for the Renewable Heat Incentive (RHI). Biogas can also be used in CHP engines.
Boilers
Biogas is 30-60% CO2, and can be burnt as long as the boiler is capable of doing so. Recovery of the CO2 from the boiler is challenging, as it requires impurities and compounds to be removed, including H2S and water. High levels of NOx and SOx are also present.
CHP
Biogas can also be used in a CHP engine, where electricity is produced from a connected generator. Heat is available from the engine for use in the glasshouse. Value can be gained from the electricity generated, heat and CO2. Subsidies on electricity production in the form of Feed-in Tariffs are available for burning biogas to produce electricity. However, unless you have already secured preliminary accreditation, any application submitted is subject to the rates available well into 2017 due to the recent introduction of quarterly capacity caps. Renewable Obligation Certificates (ROCs) are still available for generators until April 2017 and offer 1.8 ROCs/MWh for AD, with a ROC being worth £44.77; this relates to an effective rate of 8.06 p/kWh of electricity generated.
High levels of biogas clean-up are required if the gas is to be used in an engine compared to use in a boiler. This can be done using chemical or biological filters. Table 2 shows the impurities in raw biogas and their effect on engines.
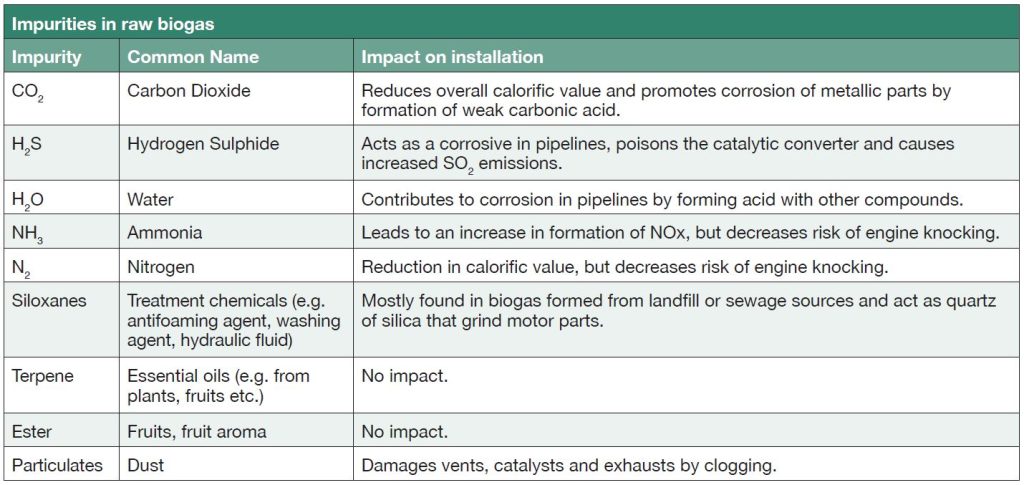
Effects of flue gases on crops
The effects of flue gases with impurities on plants are outlined in Table 3.
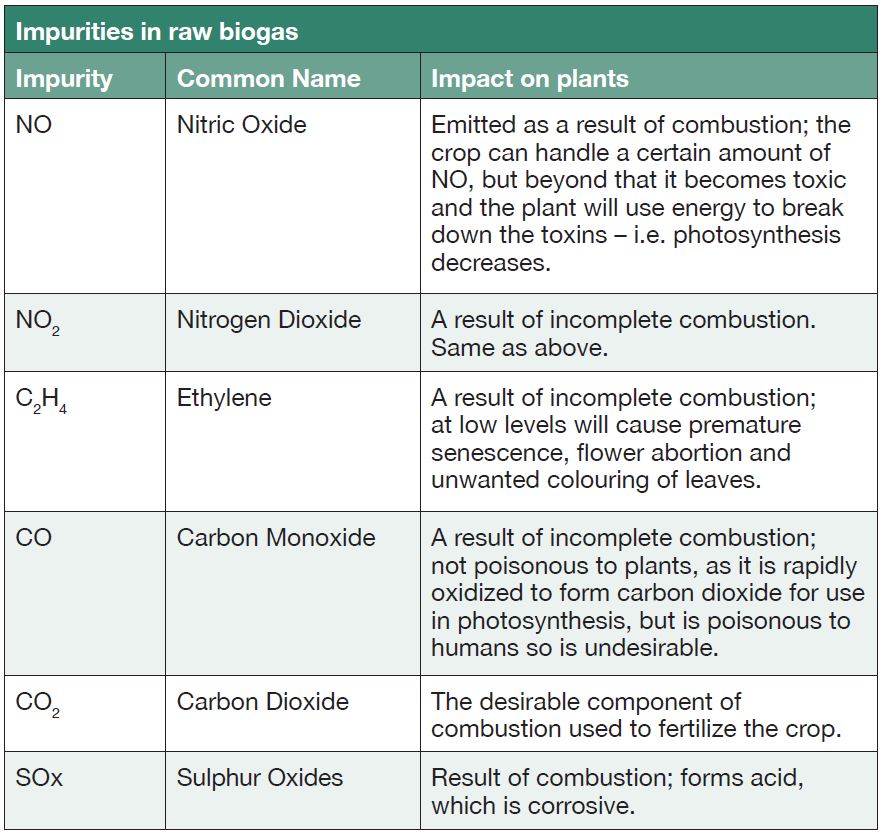
Gas cleaning
De-sulphuring equipment for biogas exhaust products is available and is in the region of £90,000/MW. Selective catalyst reduction (SCR) systems can be employed to reduce NOx, CO and a number of other pollutants and cost £300,000/MW. (Note: A 1MW system can produce about 500kg/hr of CO2.)
Note costs and data used are correct as at March 2017.
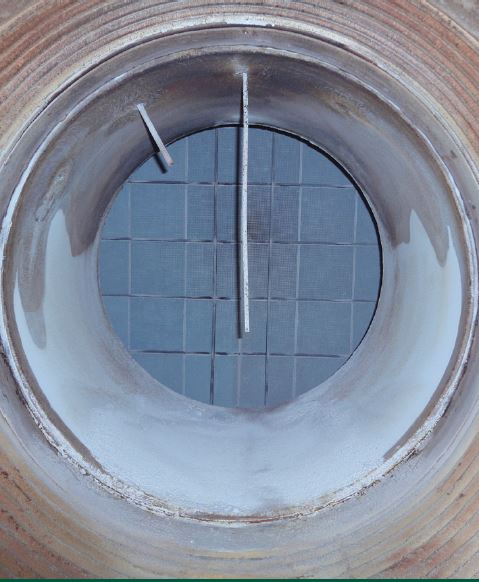
CO2 from biomass gasification
The pros and cons of stripping out and using CO2 from the gasification of dry biomass.
Gasification converts dry biomass into a combustible gas using heat in a low oxygen environment. The technology has been around since the 1800s and historically was used to produce town gas for lighting and cooking. Gasification can be carried out on any carbon source, either organic (biomass) or mineral (coal).
The gasification of biomass involves heating a biomass product (typically wood chips or pellets) to a temperature between 700°C and 1,600°C, depending on the application. This is done within a controlled oxygen environment to partially oxidise the feedstock. This breaks down the carbon source into carbon monoxide and hydrogen plus carbon dioxide. The resulting gas can then be burned in a boiler, or an engine, to produce heat and/or electricity. High levels of non-combustible CO2 are contained in the gas and can be stripped out and used. Also, following combustion, flue gases of the combustion equipment can be cleaned to utilise the CO2.
Gasification is a very scalable technology and has equipment available from quite small to very large in size. Its high temperature combustion lends itself to the production of high temperature water or steam, which can be useful for some heating/power applications. It is, however, a relatively expensive technology and requires a high quality and, therefore, high cost biomass substrate.
Subsidies are also available on energy production from gasification through the RHI (Renewable Heat Incentive) for heat and ROCs (Renewable Obligations Certificates) for electricity.
Note costs and data used are correct as at March 2017.
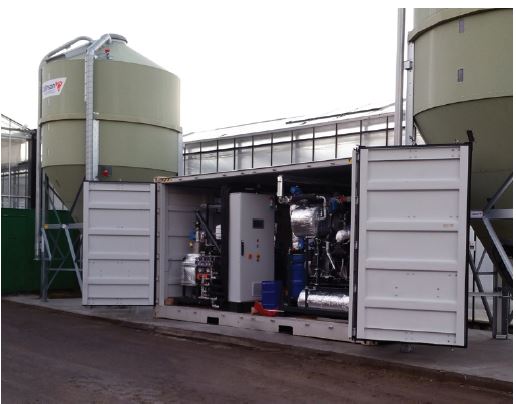
CO2 from bio-methane conditioning
How CO2 can be derived as a by-product of bio-methane conditioning and how much CO2 this method can produce at what cost.
CO2 can be derived as a by-product of bio-methane conditioning, where raw biogas (straight from an anaerobic digestion (AD) plant) is upgraded to a grid quality gas before injecting it into the national gas grid.
Biogas from AD is typically anywhere between 40-70% methane, 0-2% trace gases, impurities, water and 30-60% CO2. CO2 has to be reduced to match mains gas quality and the required cleaning process can yield significant amounts of high quality CO2, which can then be used for glasshouse enrichment.
CO2 can be removed from raw biogas using a number of methods including:
- Absorption – in water at pressure, amine solution from which CO2 can be released on heating.
- Pressure Swing Absorption – pressurised gas is led through an absorber bed, where molecules of varying sizes are removed from the gas.
- Membrane – pressurised gas is passed through a membrane system, which has selective permeability for CO2.
- Cryogenic separation – biogas is cooled until CO2 separates out as liquid form.
Electricity for the CO2 extraction plant is the biggest use for the above options; 500kWh per 500 m3/h of gas injected into the grid, which would yield a similar volume of CO2 post clean up – equivalent to about 1,000 kg of CO2. Running costs would therefore be 5p/kg CO2 or £50 per tonne.
Note costs and data used are correct as at March 2017.
You may be interested to read, Conventional sources of CO2: we look at the conventional sources of CO2 supply and discuss the influence of factors, such as heat requirement and electricity price on the cost attributed to CO2 supply.