First published May 2017
We look at the conventional sources of CO2 supply and discuss the influence of factors, such as heat requirement and electricity price on the cost attributed to CO2 supply. Conventional sources includes: flue gas from the ‘back of the gas boiler’, LPG or kerosene direct-fired heaters, CHP units or pure CO2 delivered to site.
Quick links:
- What has changed in CO2 systems?
- Natural gas boilers, CHP and air heaters
- Pure CO2 supply
- CO2 burners
- How easy is it to calculate the cost of CO2?
What has changed in CO2 systems?
In recent years factors influencing CO2 systems and economics have changed. Most significantly from the way glasshouses are heated and notably with the uptake of biomass boilers in the protected ornamentals sector. Growers of protected edibles have also embraced biomass heating and some have taken advantage of generous renewables subsidies to fund installations of anaerobic digestion (AD) plants.
Next Generation Growing (NGG) techniques have also led to a rethink of how CO2 is used, as they require changes in ventilation methods; for example, by keeping vents closed for longer the CO2 levels within the glasshouse environment are altered.
In Alternative sources of CO2, we also examine whether the supply of CO2 from alternative sources, such as biomass, is any more practical now than it has been in the past, as well as discussing the supply of CO2 from anaerobic digesters.
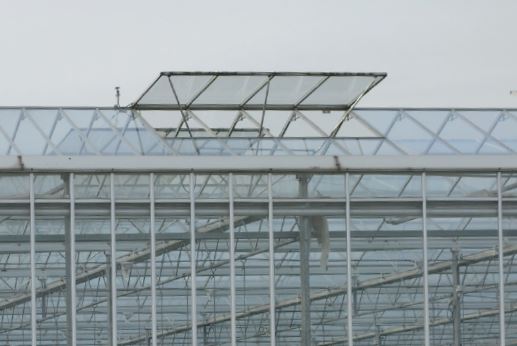
Natural gas boilers, CHP and air heaters
How CO2 production varies with how the heat is produced and why it is not always correct to see this CO2 as being ‘free’.
Considering CO2 supply from a gas boiler, gas CHP engine and air heaters, Table 1 shows how much CO2 is available from 1 kWh of gas burnt and from 1 kWh of heat energy supplied.
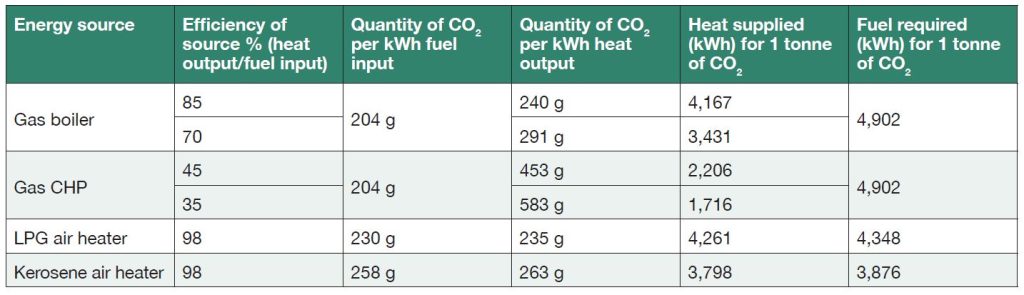
As the table shows, the quantity of CO2 per kWh of fuel input changes little with the source or the heat producing equipment. The biggest change comes from how the heat is produced and how efficiently the equipment functions. Perversely, maximising CO2 production per unit of heat produced is a result of having low efficiency equipment. This means the cost of the heat is higher than it needs to be.
CO2 that is obtained as a by-product of burning fuels for heat is difficult to put a cost on and is frequently regarded as being ‘free’, because heating for temperature or humidity control is the primary reason for burning the fuel. This is not true in all cases as some boilers will require modification, or a CHP plant will require gas-cleaning equipment to ensure the flue gases are clean and cool enough to enter the glasshouse. This is a cost that has to be factored in to derive the true price of the CO2. Using CHP as the CO2 source is further complicated by the value attributable to the electricity production.
If gas has to be burnt for CO2 production alone, with all of the heat being ‘thrown away’, its cost is related to the full fuel price. This is shown in Table 2.
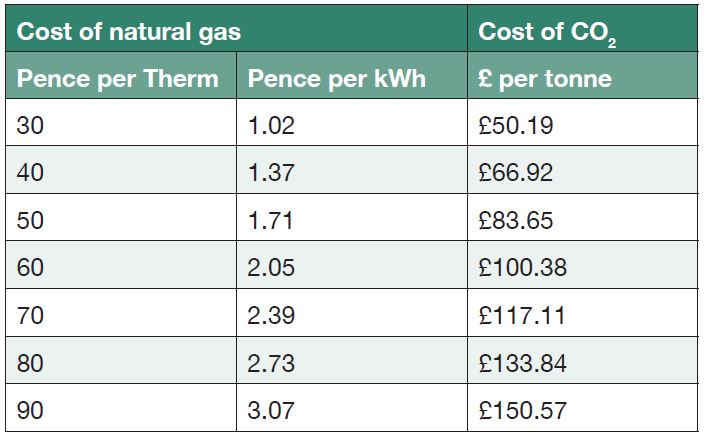
Pure CO2 supply
The factors you need to consider when using a pure CO2 supply, including the additional costs involved in using it.
Pure CO2 is produced and used by many industrial processes. As a result, there is an established market and infrastructure for pure CO2. Typical costs for pure CO2 are around £80 – £150 per tonne delivered. However, it is worth bearing in mind that there are additional costs involved:
- Tank rental and maintenance from the supplier, probably £2,000 – £3,000 per annum.
- Vaporising the liquid (typically done by re-heating), £2/tonne at today’s market price.
- Keeping the tank cool, around £1,500 per annum.
If a boiler-based CO2 distribution system is already in place, then this can also be used to distribute pure CO2. If not, then a dedicated high-pressure distribution system will be more suited to pure CO2 supply. However, a subsequent move from pure CO2 to boiler based CO2 cannot be accommodated easily, as the system will not be suitable for flue gas supply.
Note costs used are correct as at March 2017.
CO2 burners
How CO2 burners work and the comparative costs of the different fuels used – LPG, natural gas and kerosene.
CO2 burners combust LPG, natural gas or kerosene and are suspended, above the crop, within the glasshouse. The use of LPG or kerosene is more costly than natural gas, which in turn makes the CO2 more expensive. As well as generating CO2, burners produce water vapour, which can raise glasshouse humidity. They also produce heat, which will offset glasshouse heating costs in winter, but may be undesired in summer.
Regular maintenance is essential, to prevent incomplete combustion and incorrect flame temperature, since this results in the production of aerial pollutants. It may be necessary, in well-sealed glasshouses, to provide the burners with their own outside air supply. CO2 burners tend to be either on or off, giving little or no control. Their placement in the glasshouse can lead to uneven distribution and gradients of CO2. A comparison of the costs of CO2 production from different fuels is given in Table 3.
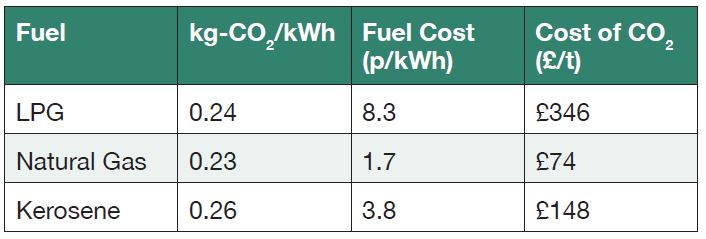
As can be seen from the table, the amount of CO2 produced per kWh is similar for each fuel type. However, the relative cost of production varies greatly, due to the market price of the fuel.
Note costs used are correct as at March 2017.
How easy is it to calculate the cost of CO2?
Apart from pure CO2, the cost of CO2 from other sources can be difficult to calculate accurately.
Whilst it is very easy to cost CO2 per tonne from pure sources, it is not so easy to quantify the running costs of the equipment needed. Similarly, the cost of CO2 from heating sources can be difficult to calculate accurately, as this is tied in to the value of the heat supplied. However, as can be seen from the figures used here, burning fuel for CO2 alone is not always particularly cost effective. As fuel prices increase, the option of buying in pure CO2 could become more attractive.
Developments in carbon capture and utilisation (CCU) technology could also be a factor. CO2 produced through industrial processes can be captured for use in manufacturing and agriculture. Since CO2 is often an undesirable by-product of many industries, there could be a plentiful supply, although the costs are still an unknown quantity.
You might also be interested in the article, Alternative sources of CO2 : we take a look at the alternative sources of CO2 supply from biomass and anaerobic digestion and discuss how they have developed since the uptake of renewable-based heating systems.