First published February 2016
Learn how to use greenhouse screens to save energy, control humidity and achieve a uniform growing environment.
Quick links:
- Screens – an essential energy saving and climate control tool
- How to overcome temperature variations
- How to improve humidity control and energy saving
The essential energy saving and climate control tool
Screens have become an essential tool for energy saving, shading and climate control in modern protected horticulture. New screen materials which save more heat energy and transmit more light have been developed, enabling screens to be deployed more in the daytime, or in double layers. There has never been a wider range of screen materials to give the optimum balance between energy saving, light transmission and shading.
In Holland, the advanced use of screens forms an integral part of HNT (or the New Way of Growing as it is known in the UK) that targets ambitious energy savings of 50% between 2010 and 2020 through the implementation of new techniques.
What has changed?
Until very recently, energy saving and humidity control were considered to be the main functions of energy screens. While those remain of paramount importance, it is becoming increasingly clear that achieving a uniform environment is now equally important. When temperature variations within a greenhouse compartment are more than 2oC, collateral effects such as increased disease risk (in cold spots where the relative humidity will be higher), wasted energy, later crop maturity and inferior quality, will occur. Growers are now advised that 2oC is the maximum acceptable temperature variation, both horizontally and vertically. Where a uniform environment can be achieved, growing at a higher Relative Humidity (RH) with less risk of condensation and therefore lower use of energy is said to be possible.
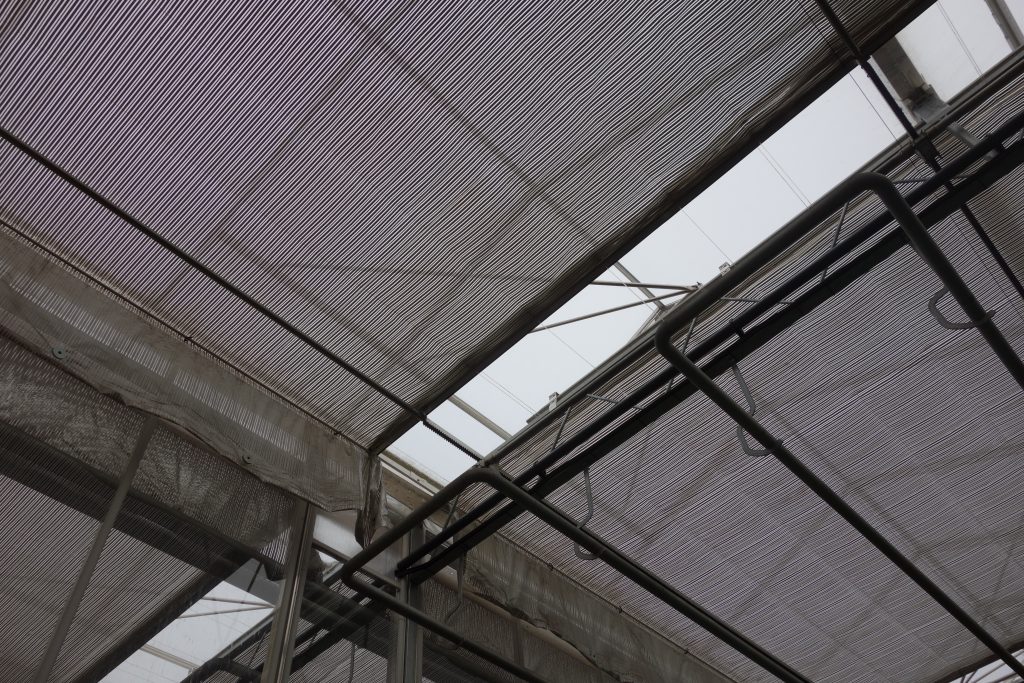
Achieving uniformity of the greenhouse environment is not easy, even in modern glasshouses with well-designed heating systems and overhead screens. In fact, the accumulation of cold, humid air above an energy screen can actually exacerbate variations in temperature when cold air from above the screen drops onto the crop through gaps where the screen may not seal properly against the greenhouse sides and gables or through holes and tears in worn screens or when gapping for humidity. However, there are now a number of practical and proven methods for overcoming temperature variations.
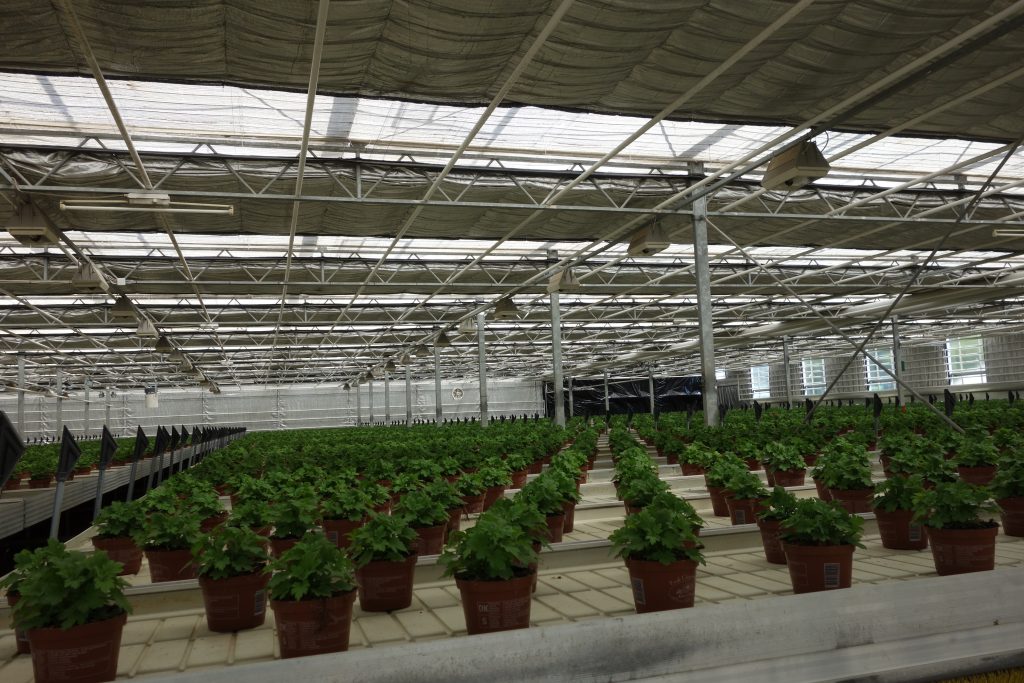
How to overcome temperature variations
We look at how installing apex seals and side screens can help even out temperature in the greenhouse.
Install apex seals
It is now widely accepted that the movement of cold air along the bay above an energy screen is a major cause of uneven temperatures. The cold air above the screen is not static and will travel to the lowest point – or find a gap – and drop onto the crop or simply create a cold spot below the screen. The installation of energy barriers (known as apex seals) consisting of transparent screen material at 30-40 metre intervals along the bay above the screen will typically reduce temperature variations by 50%.
Growers who have already installed apex seals have confirmed that the beneficial effects can be seen immediately after installation.
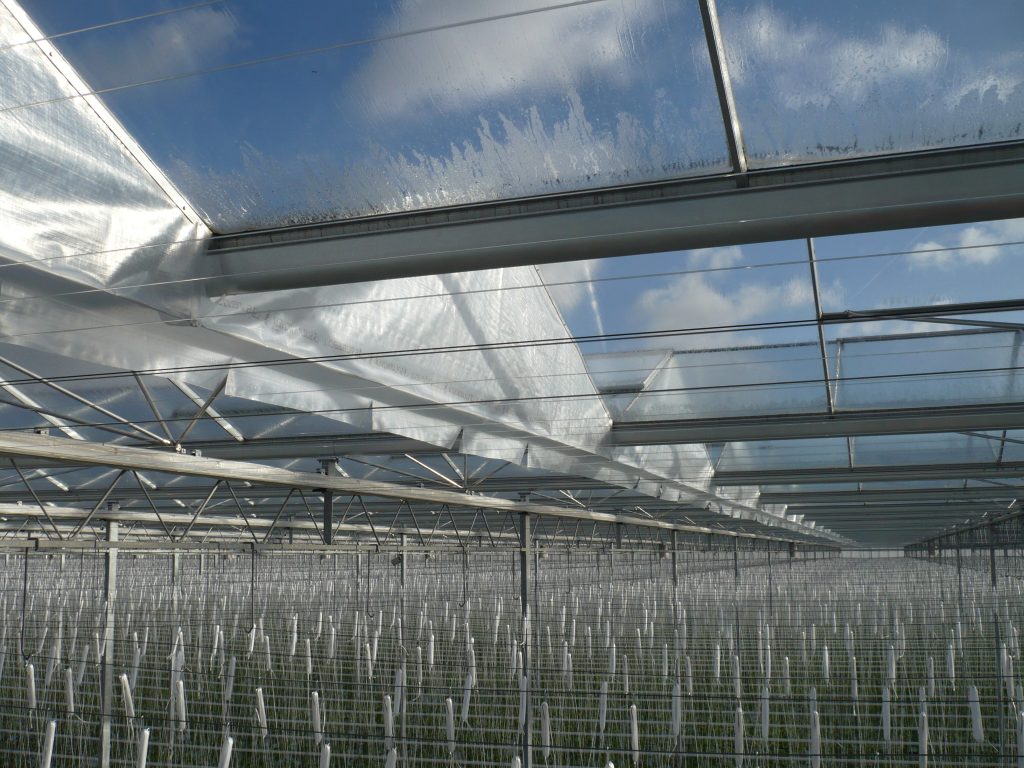
Install side screens
Irrespective of the heating system, it is likely that the maximum temperature variation in a greenhouse without side and gable screens will be greater than 2oC because warm air in the greenhouse will inevitably be drawn to the colder sides, where the resulting higher relative humidity will significantly increase disease pressure. Revenue may be lost due to the incidence of diseases such as botrytis, the cost of chemical treatment, uneven ripening and later maturity of the crop.
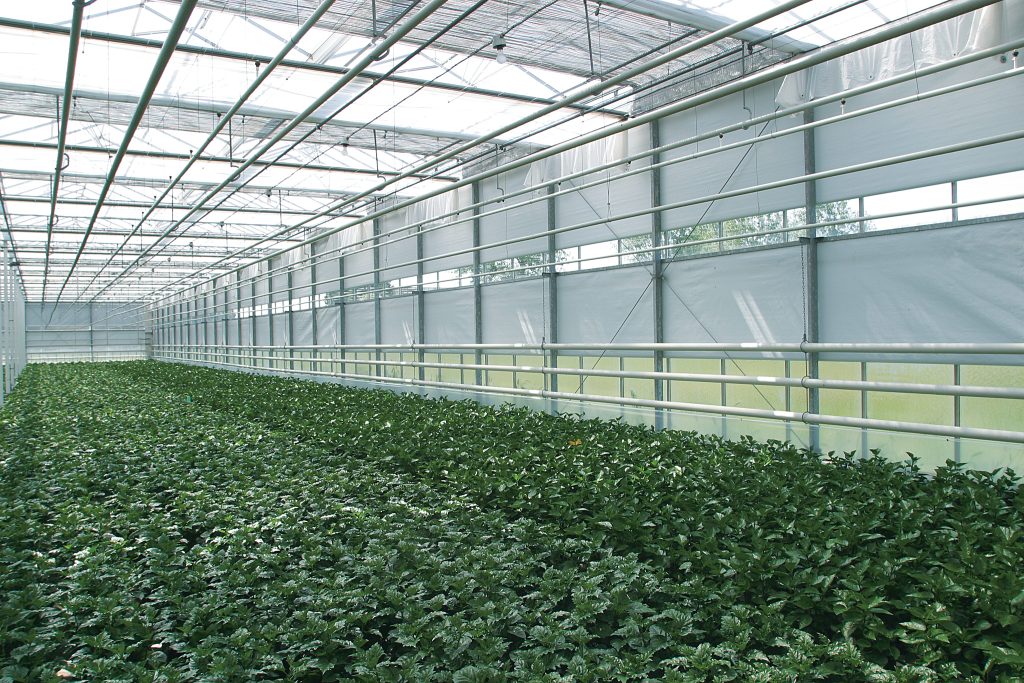
Side screens should always be used in combination with overhead screens. Although gaining in popularity in newly built glasshouses, side and gable screens have not been as widely accepted in the UK as elsewhere, mainly due to their cost when compared with temporary plastic insulation.
The amount of additional energy saving that a side screen will achieve is relative to the cumulative length of the sides and gables compared with the floor area. (So a 1 Ha greenhouse with side screens will benefit from more energy saving proportionately than a 2 Ha greenhouse).
Glasshouse post height | 5 metre |
Side screen cost | £70 per metre |
Energy saving | 12.5 kWh/m2/year |
Payback | 10 years on gas savings alone |
Table 1 demonstrates a lengthy payback on energy costs alone, however when the negative consequences of uneven greenhouse temperatures are also taken into account, the payback time for investment in side screens is likely to be much less, and explains why most new greenhouses are now fitted with side screens at the outset.
How to improve humidity control and energy saving
The practical steps and changes that can help improve humidity control and save energy in the greenhouse. We consider gapping, the increased use of daylight, doubling up, clear or diffuse light, and wear and tear.
Reduce or eliminate gapping for humidity control
It has been standard practice to gap the overhead energy screen when humidity levels below the screen are higher than desirable. However, breathable screen materials make it possible to reduce humidity through the closed screen by venting above it. Keeping the screen closed not only saves energy, but prevents cold air dropping onto the crop, reducing local air movements and undesirable cold and warm spots in the process.
The installation of an aspirated measuring box above the screen is now worthy of serious consideration, to provide the grower with very useful additional information about the roof space temperature and humidity and to influence the screen opening strategy.
Increase daylight use
There is scope for achieving higher energy savings by using energy screens for longer because materials are now available with very high light transmission (88%-89%).
These more transparent energy screens give growers the option to use the screens during parts of the day as well as at night. Knowing how to take full advantage of longer screening hours without loss of yield or quality is a very specialist area requiring expert advice and support, but properly implemented can lead to additional energy savings of between 7-12% (Ruijs, Reijnders, Kempkes & Esmeijer 2005).
In very cold weather, rapid heat loss to a clear sky is a common cause of condensation in the crop canopy. Installation of an irradiation sensor (pyrgeometer) enables the screen to be closed earlier in such conditions, so that rapid heat loss and condensation can be avoided.
One leading manufacturer has developed a new range of materials which they claim encourages the formation of a thin film of moisture rather than water droplets under the screen They say that this allows even higher light transmission for daylight use of the screen.
Should you double up?
While the use of double screens in Holland has increased to around 100 hectares in just 5 years, the practice has yet to make an impact in the UK.
A double screen will not save twice as much energy as a single screen, this is because the second screen will be deployed less often than the first. Use of single screens can reduce energy consumption by up to 47% with new materials and where they are well fitted. Fitting an additional screen will increase this energy saving to 63%.
Screens only save energy when closed, so there will be no energy saving when the screen is fully open and reduced energy saving when the screen is gapped or if the material is suffering wear and tear.
Clear or diffuse light?
The energy saving properties of modern screen materials benefit all high energy crops, but will have different light transmission properties. Some crops benefit from diffuse light, especially in summer when some shading is required, others require no shading and respond very well to maximum light transmission at all times.
Peppers, strawberries and most ornamental crops respond very well to diffuse light while tomatoes benefit from maximum direct light, so it’s important to consider which screen material will provide the best combination of energy saving and light quality.
Address wear and tear
Energy screens have been in widespread use for many years, so many existing screen systems which were installed quite a few years ago will not benefit from the energy saving or light transmission properties of the latest screen materials. The constant use of the screens over thousands of operational hours not only results in tears and gaps in the material, which reduces their energy saving potential, but also accumulates dirt and grime (which makes daytime deployment inadvisable as light transmission is reduced).
Screen suppliers claim that screens can lose 2-3% of their energy saving and light transmission properties annually due to wear and contamination.
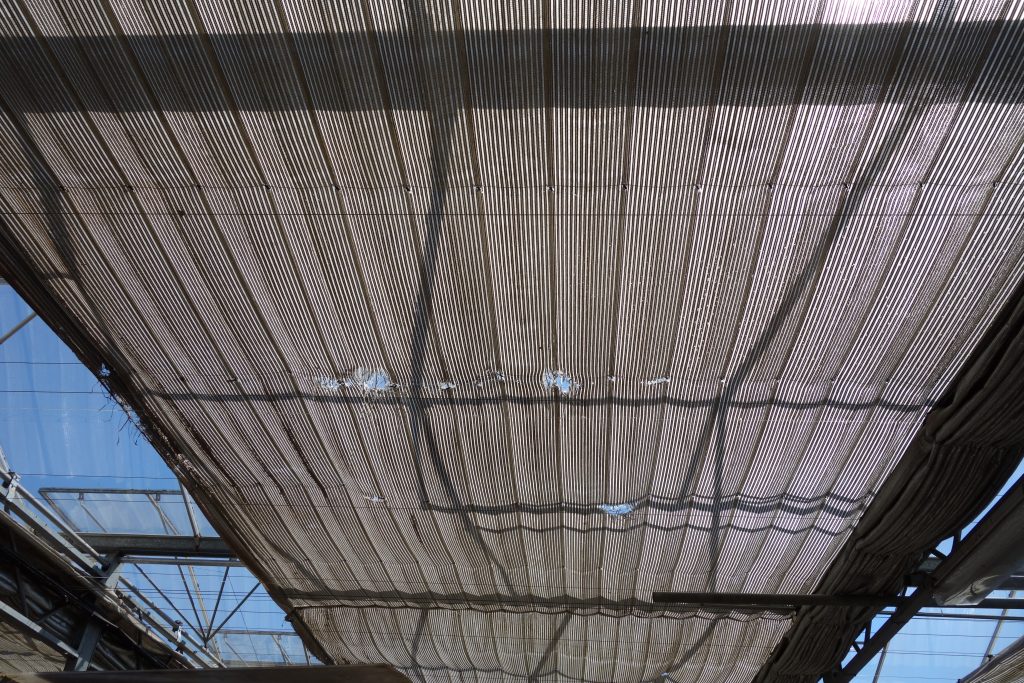
In most cases, the existing mechanical parts of the screen system (motors, pulleys and wires) will be serviceable even after a number of years, so replacement of the old screen material will bring the whole system up to a modern standard. The cost of replacement will vary depending on the age and dimensions of the greenhouse, but will typically be in the region of £2.50/m2.
Old screen energy saving | 37% when installed 30% after 10 years |
New screen energy saving | 47% |
Additional Energy saving | 25 kWh/m2/year |
Cost of replacement | £2.50/m2 |
Payback | 5 years on gas savings alone |
Other developments
Supplementary lighting installations are now commonplace and planning authorities will usually insist that light spillage to the area surrounding the greenhouse is prevented by the mandatory use of a light pollution or blackout screen. In many cases, growers would prefer to have the option to use an energy screen at certain times and a light pollution or blackout screen when the lights are on or when they need to create short days.
In the past, two separate screens systems have been required, each with its own motors, gearboxes and support wires. Now it is possible to install a system with both energy saving and light pollution or blackout material on the same layer and deploy one or the other automatically when required, thereby saving on the cost of one mechanical screen system. The same principle can also be applied to side screens, which can be particularly useful on the southern aspect of the greenhouse.