First published August 2017
Sensors are fundamental to the effective control of the glasshouse environment. Learn what to look out for to avoid inaccurate measurements which can result in wasted energy and poor crop performance.
Quick links
- Critical control system components
- Wireless technology and cloud based control
- Sensors for temperature and humidity
- Sensors for light and vent position
- Sensors for CO2, pH and crop weight
- Other uses for sensors
Critical control system components
Sensors are the eyes and ears of your control system and fundamental to its operation. Inaccurate measurements, due to faulty or poorly maintained sensors, can result in wasted energy, substandard crop performance and even increased disease so they are very important. In this technical update, we discuss what to watch out for when choosing and looking after sensors in glasshouses.
We are grateful to Priva, Hoogendoorn, Grodan and CMW Horticulture for their assistance in providing images for this Technical Update.
Wireless technology and cloud based control
Until recently, both analogue and digital sensors have been connected to monitoring and control systems by cable, with data used locally. However, the development of more reliable wireless technology, together with improved networking, means that more wireless sensors are being used.
Leading companies are very active in thinking about how wireless sensors connected to central systems and, in turn, the internet can act more interactively in what have been termed Cloud based systems. Field equipment already uses this type of technology to automate and control harvesters, sprayers and drills. Storage and processing of data from many sensors and sites brings the possibility of more integrated and informed control, so shared intelligence and high level, real-time intervention can improve system and plant performance.
Sensors for temperature and humidity
What to look out for when measuring heat, air and crop temperatures and the use of wet and dry humidity sensors and electronic humidity sensors.
Temperature
Temperature is probably the most common condition measured in glasshouses and covers heating systems as well as air and crop temperature measurements.
Most conventional sensors these days are electronic, either resistance based or thermistor. Stability and accuracy are good with these sensors, although it’s important to occasionally use a second sensor to check for drift.
Sensors fail from time to time and, when they do, it’s usually quite obvious. In these cases, the control system to which they are attached will normally alarm.
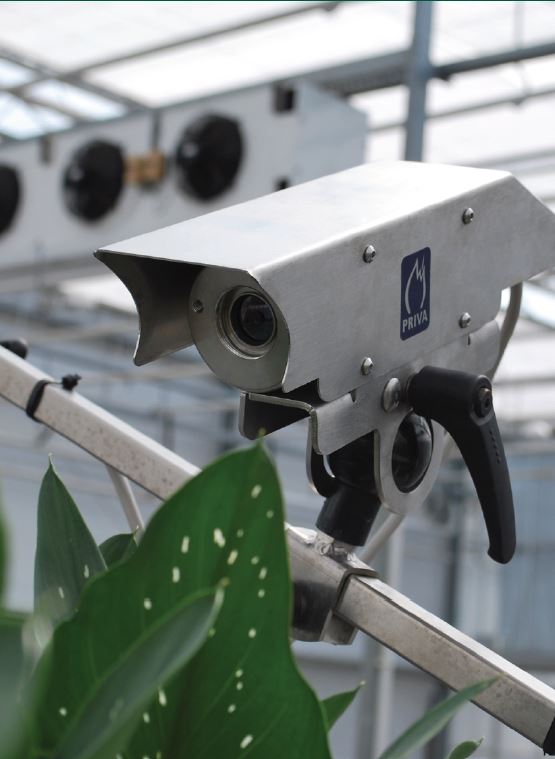
Plant temperature
Infra-red cameras have been used to monitor plant temperature for more than a decade now, but uptake has been slow in the UK. This is because of relatively high costs and the absence of user friendly applications to integrate the produced data into the environmental control system. However, that is changing now, with Priva and Hoogendoorn both offering solutions in which the infra-red camera plays an integral part in control.
Foliage, fruit or flower temperature can indicate when the plant is under stress, or when the dew point is reached, and provides the grower with useful additional information about the environment. The temperature data can also be used to calculate Vapour Pressure Deficit (VPD).
Humidity
Wet and dry humidity sensors
Humidity measurements are derived from the comparison between two identical temperature sensors, one of which is kept dry and the other moistened by distilled water on a sock or wick. The evaporation of water from the wick lowers the temperature, so that the wet bulb thermometer shows a lower temperature than the dry bulb thermometer. The humidity is calculated from the difference between the dry and wet bulb measurements.
Wet and dry bulb humidity measurement is both accurate and reliable, as long as the wet bulb is kept moist with clean distilled water. The most common errors are due to contaminated water or wick, or even no water at all, so regular checks are important.
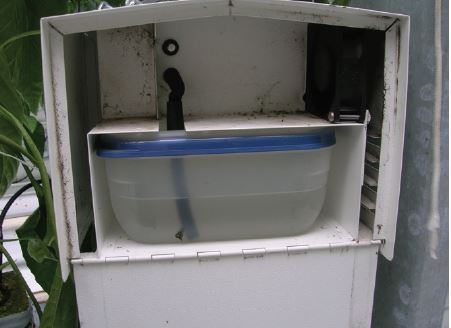
Electronic humidity sensors
These eliminate the need for a water supply, so would seem to be an ideal replacement for wet and dry bulb measurement. However, they have their limitations. The sensors are less robust and must be replaced at regular intervals, typically every one or two years, as their accuracy deteriorates over time. Furthermore, they are less accurate at high Relative Humidity (RH).
Measuring boxes
Temperature and humidity sensors must always be contained in an aspirated enclosure (e.g. a measuring box), so that the effect of direct radiation is eliminated.
Sensors for light and vent position
What to look out for when using different types of sensor to measure light and how to measure or estimate vent position based on ‘time’ or, more accurately, by using a potentiometer.
Light
Every environmental control system will include a weather station with a light sensor measuring either:
- Visible light (Linear light)
- Radiation (e.g. Kipps Solarimeter)
- Photosynthetically Active Radiation (PAR) – the spectral range (wave band) of solar radiation from 400 to 700 nanometres used in photosynthesis
PAR sensors are the most reliable indicator of the section of the light spectrum which is useful for plant growth.
Some growers also install internal light sensors and, with the advent of Next Generation Growing (NGG) techniques, there is some interest in sensors to measure radiation loss from glasshouses.
A pyrgeometer measures near-surface, infra-red radiation loss at wavelengths in the region of 4.5 μm to 100 μm. In the glasshouse sector, pyrgeometers are used to detect rapid heat loss at night under clear skies and trigger the early deployment of thermal screens.
Vent position
Accurate vent position is a critical component of modern environmental control, so it must be measured or estimated. It is possible to estimate the vent position based on:
- Time – Using the time taken for the motor to open the vents from fully closed to fully open as a base reference.
- Direct measurement – Using potentiometers, either fitted to a pendulum attached to the ventilation window, or by a potentiometer in the gearbox which operates the ventilation system. This tends to be the most accurate system.
In both cases, a potentiometer is calibrated by a technician at fully closed and fully open, and the control system uses the resulting reference to calculate a percentage between the two.
Whichever system is used, it is essential that limit switches are also incorporated to prevent damage in the event of sensor failure.
Sensors for CO2, pH, and crop weight
What to look out for with centralised and distributed CO2 measurement, the use of pH sensors and crop weight as an indicator of crop performance.
CO2
Centralised CO2 sensors were the mainstay of environmental control systems for many years. They rely on pumped air samples, using multi-channel manifolds with switching solenoids for multiple glasshouse zones. They require regular calibration using reference gas samples, but are reliable and accurate.
With the miniaturisation and cheapening of sensor technology, these systems are gradually being replaced by distributed systems, which are based on a network of sensors, each having local processing. The calibration of electronic CO2 sensors drifts over time and can only be corrected using specialist calibration equipment. Furthermore, in some cases, the manufacturer will not guarantee accuracy in RH conditions over 80%, so it is advisable to ask for the manufacturer’s specification where RH is likely to be high, to ensure that the correct sensor is installed.
pH
pH measurement is widely used in UK horticulture to control acid dosage in order to reduce pH levels of water or nutrient solutions. The pH sensors may be portable or incorporated within an irrigation or dosing system.
All pH sensors measure the potential difference (voltage) between two electrodes encapsulated in an aqueous solution or gel. The voltage generated between the electrodes varies depending on the hydrogen ion concentration (acidity) in which the sensor is immersed.
Although various types of sensor are available, they share some important characteristics:
- Generally quite fragile.
- Sensors for various operating pressures are available – it is essential to use a pH sensor within its rated pressure range.
- Weekly calibration required – using standard solutions of at least two known pH levels is advisable.
- Limited shelf life – should not be stored for more than six months after manufacture.
- Failures are common – every pH control system should incorporate adequate safety measures to guard against acid overdose in the event of sensor failure.
- Should be replaced annually.
Crop weight
For vine crops grown in substrate, such as tomatoes, the continuous measurement of the combined weight of the plant, fruit, substrate and water content is regarded as a useful tool in determining crop performance.
It is possible to draw conclusions about how the crop is responding to the environment by tracking the combined weight of the contributing elements and plotting them graphically against other crop data, such as irrigation applications, and climate components. This will also show how the environmental computer settings may need to be adjusted to improve crop performance.
Several manufacturers offer systems for the measurement of crop weight. Two measurement principles predominate:
- Crop trays resting on a frame incorporating load cells, on which two or more substrate slabs are placed. Normally with one tray per climate zone.
- Multiple weighing devices per climate zone, from which the vines are suspended, communicating wirelessly with a central data server.
Other uses for sensors
A look at some other uses for sensors in the glasshouse and the key things to consider about each.
Screen position
Screen position is accurately controlled using a signal generated by a potentiometer in the screen gearbox, using exactly the same principle as for measured vent position. Accurate control of screen position will undoubtedly become more important with the deployment of NGG techniques, so the use of potentiometers to measure screen position is likely to become more widespread.
Electrical conductivity
Electrical conductivity is a convenient measure of the concentration of salts (inorganic fertiliser) in irrigation water, soil or substrate solution. It is essential that the system or instrument incorporates temperature compensation, as the conductivity of a solution is very temperature dependent. The sensors are generally robust and do not require routine calibration. However, the electrodes should always be kept clean and it is good practice to periodically check the measurement with a good quality, portable meter.
Drain volume
Drain volume is measured by a conventional flow meter (rated for nutrient solution) or by a micro measurement device such as a ‘tipping spoon’ connected to a micro switch. This can either be done at a micro level, where the volume of drain water from just a few plants is measured, or it can be done for part or all of the crop. By and large, drain measurement on a micro level is faster and allows immediate response to variance in the amount of drain. Drain collection from a row, bay or whole crop will be more accurate, but information is slower to assimilate.
Moisture content
Various sensors are available for the measurement of moisture content in soil, composts and substrates, both portable and fixed. Most of the commercially available sensors rely on probes inserted into the substrate at several locations in the greenhouse (typically three or more). It is critical that probes are installed strictly in accordance with the manufacturer’s recommendations. Several suppliers also offer sensors specifically for use with substrate, which combine water content data with conductivity.
O2 measurement in the root zone
Avoidance of overwatering in substrate is topical, not only because waste of water and fertiliser is expensive, but also because the oxygen depletion (which is often a result) can cause root death. So, measurement of the oxygen content in the root zone is helpful. Though not widely available yet, sensors for O2 measurement in soil are being developed.